In scenarios such as construction, gardening, and agricultural production, small excavators have become important tools due to their flexible and efficient characteristics. However, their complex mechanical structure and high-frequency operation requirements place extremely high demands on daily maintenance. This article provides a refined maintenance plan from the three dimensions of "daily inspection - periodic maintenance - in-depth maintenance" and combines the characteristics of the core components of the equipment to help you extend the life of the equipment and reduce the risk of failure.
1. Before starting the engine every day: 6 core components "morning inspection"
1. Engine system: "heart check" before starting
Oil level and status: Pull out the oil dipstick and observe that the level should be between the upper and lower scale lines. If the oil color is emulsified or dark black, it needs to be replaced immediately (normal oil should be translucent brown-red).
Coolant and antifreeze: Check the expansion pot level when the engine is cold. If it is lower than the MIN line, add coolant of the same brand. In winter, the freezing point needs to be tested (it is recommended to use -40℃ antifreeze in areas below -25℃).
Air filter cleaning: Take out the paper filter and blow it from the inside to the outside with compressed air (note that it cannot be washed with water). If the surface is damaged or the pores are blocked, it needs to be replaced immediately (it is recommended to replace it once every 200 hours).
2. Hydraulic system: prevent "blood vessel blockage"
Hydraulic oil level: After idling for 5 minutes, turn off the engine and observe the oil level gauge of the hydraulic oil tank. The level should be between the H-L scale. When it is lower than the L line, add the same type of anti-wear hydraulic oil (such as ISO VG46).
Pipeline leakage inspection: Before starting, bend over and observe the hydraulic pump, cylinder, and oil pipe interface. If there are oil stains or oil drops (even slight oil leakage), tighten the joint with a torque wrench according to the standard torque (usually 15-25N・m). If it is serious, replace the seal.
3. Chassis and walking system: "Foot care" of grounding parts
Adjustment of track tension: After starting, run at idle speed, drop the bucket to the ground, and observe the track droop (ground clearance). Normally, it should be 30-50mm. If it is too loose, add grease through the tensioning cylinder (3-5 times per track, 10 seconds apart each time). If it is too tight, release the grease.
Lubrication of supporting wheels and sprocket wheels: Use a grease gun to add lithium-based grease to each lubrication point of the chassis (usually 8-10 oil filling ports on each side) until the old oil is squeezed out (it is recommended to lubricate once a day before operation).
2. Weekly in-depth maintenance: 8 key items "System maintenance"
1. Engine belt group: Prevent "power breakage"
Multi-V belt/V belt inspection: After stopping, press the middle of the belt with your thumb, and the deflection should be between 10-15mm (too loose will cause insufficient speed of the generator and water pump, and too tight will increase bearing wear).
Observation of the belt surface: If cracks, hair loss or edge wear occur, replace them in groups (do not replace only one piece to avoid uneven tension). After replacement, use a special tool to adjust the tensioner to the standard torque (refer to the equipment manual).
2. Fuel system: Clean the "digestive system"
Replace the fuel filter: first close the fuel valve, loosen the oil pipes at both ends of the filter (note to use a container to catch the leak), unscrew the old filter, apply a small amount of engine oil on the new filter seal, tighten it counterclockwise (torque: 20-30N・m), start the rear exhaust air (press the hand oil pump several times until it hardens).
Drain the fuel tank: open the drain valve at the bottom of the fuel tank to drain the deposited water and impurities (normal fuel should be clear without turbidity. If the water content is high, check whether the fuel tank cap seal is damaged).
3. Cooling system: ensure "body cooling"
Radiator surface cleaning: use compressed air to blow from the back of the radiator (avoid using high-pressure water gun to prevent deformation of the radiator). If there is oil stain, use special water tank cleaning agent (circulate for 20 minutes after dilution, and then rinse with clean water).
Fan coupler detection: After starting, run at idle speed. When the water temperature rises to 80℃, the fan should make an obvious "buzzing" sound (coupler engagement). If there is no sound, check the silicone oil level or replace the coupler.
4. Electrical system: Maintain the "neural network"
Battery maintenance: Use a multimeter to detect the voltage (12.6V or more when unloaded, 13.5-14.5V after starting). If there is white oxide on the electrode head, rinse it with hot water and apply vaseline. The connecting wire must not be loose (torque: 8-10N・m).
Wire harness inspection: Along the line direction of the engine, cab, and operating table, check whether the insulation layer is damaged and whether the connector is oxidized. Focus on checking the wiring harness at the rotating part (which is easily damaged due to rotational friction).
3. Monthly/quarterly in-depth maintenance: 5 professional-level "organ maintenance"
1. Hydraulic oil quality inspection: prevent "blood pathology"
Oil sampling and analysis: Use a special sampling bottle to collect oil samples at the hydraulic pump outlet, observe the transparency (turbidity indicates water or impurities mixed in), test the viscosity (change more than ±10% compared with new oil requires replacement), and it is recommended to send it to a professional organization for contamination inspection every 500 hours (NAS level should be ≤9).
Hydraulic oil tank cleaning: Clean the oil tank thoroughly every 2000 hours. First use dough to remove dust from the inner wall, then wipe it with silk cloth (do not use cotton gauze to prevent fiber residue), and replace the oil tank breather filter (usually red sponge-shaped, replace it when it turns black).
2. Cylinder and seal: Prevent "joint oil leakage"
Piston rod cleaning: After operation, wipe the surface of the cylinder piston rod with a soft cloth. If there are dirt particles, clean it with diesel to avoid scratching the seal (must be done after daily operation).
Seal replacement cycle: Depending on the operating environment, generally replace the cylinder dust ring every 1000-1500 hours, and replace the main seal every 3000 hours (special tools must be used during replacement to avoid seal distortion).
3. Transmission and drive axle: Protect "power transmission"
Gear oil replacement: Drain the oil when the car is hot (to facilitate the discharge of impurities), use a gear oil replacement machine to extract the remaining old oil, add the same model GL-5 85W/90 gear oil (the liquid level is based on the overflow of the refueling port), and check the liquid level after driving 5 kilometers after replacement.
Differential lubrication: Check the wear of the differential gear through the observation hole. If there are pitting or cracks on the tooth surface, repair it in time. If the grease is insufficient, use a high-pressure grease gun to add it (until it overflows from the exhaust hole).
4. Operating device: Calibrate the "control center"
Adjustment of the free travel of the joystick: After starting, run at idle speed and measure the free travel of the joystick (front and back/left and right should be ≤5mm). If the travel is too large, adjust the tie rod ball nut (tighten clockwise to shorten the travel, and test run after each adjustment).
Dashboard function test: Test the tachometer, water temperature gauge, fuel gauge, and warning light in turn (short press the test button, all indicator lights should be fully lit). If an indicator light does not light up, check the fuse or sensor connection.
IV. Response to special working conditions: 3 types of scenarios "customized maintenance"
1. Cold areas (below -10℃)
Preheating before starting: Use the engine water jacket heater (power 500W, powered on 2 hours in advance), replace low-freezing point oil (such as 0W-40) and diesel (-35#).
Battery insulation: Install an insulating cotton sleeve and charge after work every day (to avoid low temperature and power loss).
2. Dusty environment (such as mines, deserts)
Air filter upgrade: install a pre-filter (desert filter), blow the filter every 50 hours, and replace it every 200 hours (500 hours in normal environment).
Radiator protection: install a dust screen (30-50 mesh), and blow the dust off the screen after each shift.
3. Wading operation (water depth exceeds 1/2 of the track)
Waterproof treatment: Check whether the waterproof rubber sleeves of each electrical connector are intact before wading, and install a waterproof cover on the exhaust pipe (wrap it with a plastic bag and tie it tightly).
Post-operation maintenance: Immediately after the operation, clean the chassis mud and sand, add butter to the travel motor and slewing bearing (to drain the infiltrated water), start the engine and run it at idle speed for 30 minutes to dry the internal moisture.
5. Maintenance records and tool management: Building "equipment health files"
Maintenance records: record the time, items, replacement parts and consumables of each maintenance (it is recommended to use Excel spreadsheets or special APPs, and set expiration reminder functions).
Special tools: equipped with torque wrenches (accuracy ±5%), hydraulic oil testers, digital multimeters, etc., and calibrated regularly (once a year) to ensure data accuracy.
Accessory reserves: according to the intensity of the operation, reserve commonly used vulnerable parts (such as filter elements, seals, fuses), and store them in a dry and ventilated place (avoid direct sunlight and moisture).
Conclusion: Maintenance details determine the life of the equipment
The maintenance of small excavators is not a "formality", but a "precise care" for each component. From the "millimeter-level" inspection of daily morning inspections to the "systematic" maintenance of monthly maintenance, every detail directly affects the reliability and economy of the equipment. It is recommended that operators strictly follow the principle of "prevention first, prevention and treatment combined", incorporate maintenance into daily work processes, keep the equipment in the best working condition, and escort construction efficiency and safety. Remember: every bit of your care for the equipment will be transformed into long-term and stable operational returns.
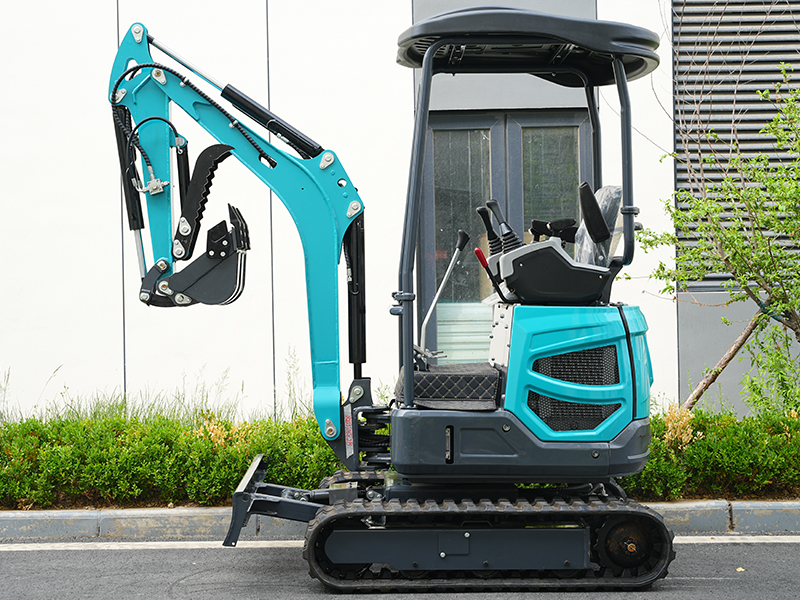